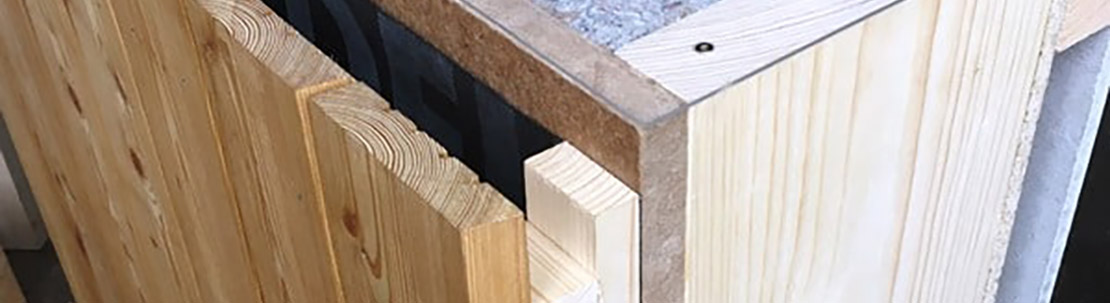
The basic element of all prefabricated houses are the panels. In this post we share insights on what makes a good exterior wall panel and what choices and tradeoffs a client might face when making choices on price and performance.
Exterior wall panels
As a part of the building envelope, exterior walls primarily are necessary to provide structural stability and maintain a suitable microclimate inside by protecting from the exterior elements such as wind and precipitation, heat, cold, sunlight.To do this the envelope must be well insulated, weathertight and airtight. The make-up of panels is usually described in “layers”. External walls typically have the most layers compared to roof, floor and interior wall panels with each of these layers playing an important role. Let’s go through them beginning from the interior of the house.
Interior surface
Interior wall surface is usually made of drywall. For more robustness and stability an additional OSB or plywood layer could be used. This is a layer that customers sometimes opt not to have in order to decrease the cost of the project. But this layer noticeably improves the living experience of the resident of the house – with the boards the wall surface cannot be broken by simply smashing into it and cabinetry and shelves can be securely screwed to the walls. Plywood is used if the client wants extra rigid walls but plywood is more expensive than OSB. Another alternative is to use gypsum fibreboard which is significantly more durable than drywall and can deliver similar performance as the combination of drywall and OSB.
Using drywall or gypsum fibreboard allows the manufacturer to close up the walls at the factory while using other materials would mean that only open walls can be delivered. For a more traditional feel, for example in holiday cabins, clients sometimes opt to use wooden siding boards. The tradeoff of installing interior wood board siding (that can be pre painted) on-site versus having to render and paint the drywall on site (electrical conduits and sockets can be pre installed) should be weighed.
Service area
The service frame provides an area for electrical conduits and sockets to be laid in the wall without penetrating the vapour control layer and providing additional insulation thickness for better energy efficiency.
Some manufacturers offer much cheaper panels without this layer cutting down on the cost of the panels. However it would be a very bad idea to omit the service area because that would mean penetration in the vapour control layer at each electrical socket where special sockets should then be used requiring meticulous work and providing many possible points of failure when the house is in use. You would not believe the amount of water that can build up in the walls in cold climates through condensation when the vapour control layer has a breach!
The service frame is made of 45 to 50 mm laths for a reason – having it thicker could create a dew point whereby creating a risk of moisture build up in the layer that can cause mold to form in the walls which is bad for the wall and the health of residents.
Since interior surface and service area layers are after the vapour control layer they can essentially be considered inside the house so off-gassing from these materials should be considered. Some insulation and sheathing materials that contain formaldehyde should preferably be avoided.
Vapour control layer
The vapour control layer is what makes the walls airtight and prevents moisture from building up inside the wall that can damage wood structures and grow mold. These problems arise if excessive humidity from inside the house passes through the wall and condensates inside it when it meets a cold layer of the wall. Also an airtight building is energy efficient because it requires less energy to keep it warm in winter and cool in summer to compensate for air leakage.
The manufacturer should be able to describe their method of making this layer airtight e.g. what materials are used and how seams are closed.
Framing and insulation
The structural frame and main insulation layer makes up the core of the wall. Having this layer 245 mm thick provides excellent energy efficiency and sound insulation for the best indoor comfort.
A typical wall is insulated with mineral wool. A more climate friendly option is using cellulose or wood fibre wool that has a smaller ecological footprint, provides even temperature throughout the day due to larger thermal inertia and allows the panel to be humidity permeable letting excess indoor humidity to pass through to the outdoor environment.
Wind protection
Wind protection boards and wind barrier membrane protect the core of the wall from heat loss due to wind. Requirements for these layers differ across countries – some require wind protection boards, some a wind membrane, others require both. So it is advised to consult the architect to inform the manufacturer when ordering to a country that is not a main export market. Wind barrier that is water vapour permeable should be preferred to allow the wall to dry out in case there is accumulation of moisture in the wall due to damage during use of the house.
Facade siding
Vertical wood laths create a space for facade ventilation that protects the house from sunlight heat and also seals the wind barrier. There are many options that can follow this layer depending on the architect’s wishes. Most common facade finishes are:
- horizontal or vertical wood siding boards
- stucco
- cement fibreboard
- plastic boards
- metal cladding
- Some less frequently used finishes are tiles, bricks, wood shingles.
There are many options for each of these facade finishes easily reaching hundreds of possible solutions. This is the part that is most up to the wishes of the architect and client. The costs of each option can differ very significantly so clarity when specifying the desired solution is important. Misunderstandings can be avoided by including photos of examples of desired facade finish to the price request.
The most common and cost efficient option for a facade is two times painted horizontal wooden cladding. Some types of finishes require varying amounts of on site work so keep in mind that any work executed on-site will cost you more money when choosing the facade siding option. Vertical wood board cladding can only be installed on-site and requires installing additional laths on-site.
When choosing wood there are several options to choose from regarding the type of wood, the shape of the boards and the type of treatment. Options for wood treatment are:
- natural (untreated)
- painted
- stained
- thermally modified
- impregnated
The type of wood used for siding usually is regular pine. Costlier but longer lasting Siberian larch boards are chosen for the naturally aged wood look. Also choosing a non-standard shape of siding boards will increase the price.